In the paper and pulp industry, water treatment plays a critical role in ensuring smooth operations and maintaining product quality. During production, the process water often generates excessive foam due to the presence of surfactants, fillers, and chemical additives. If not controlled, foam can lead to overflow, pump cavitation, reduced drainage efficiency, and increased maintenance costs. This is where defoamers become an essential solution, helping mills stabilize their systems and achieve greater production efficiency.
Among the various solutions available, Rickman defoamer stands out as a trusted choice for the paper and pulp industry. Its formula is tailored to the specific challenges of pulp water systems, delivering excellent foam suppression with long-lasting effects. Beyond the product itself, Rickman provides comprehensive technical support, fast delivery, and customized application guidance, ensuring that every client can maximize efficiency and minimize downtime. This combination of reliable product performance and dedicated service makes Rickman a strong partner for businesses seeking both productivity and sustainability.
Click on the related products links:RK-F0080(High Efficiency Fatty Alcohol Antifoam)/RK-800P(High Cost-effective Defoaming Agent For Concrete)
Enhancing Ink Production and Printing Quality with Effective Defoamer Solutions
In the ink manufacturing and printing industry, foam generation is a common challenge during mixing, grinding, filling, and application. Foam can trap air in the formulation, cause surface defects, and disrupt ink transfer during printing. Whether in water-based, solvent-based, or UV-curable inks, uncontrolled foam can lead to poor print quality, slower production speeds, and increased waste.
In addition to product performance, Rickman provides strong technical support, responsive customer service, and reliable global supply. Our experienced team works closely with ink manufacturers to optimize formulations, conduct performance testing, and ensure consistent results. With Rickman, customers not only gain superior defoaming technology but also a committed partner in enhancing productivity and product excellence.
Click on the related products links:RK-980P(Good compatibility Defoamer)/RK-73T(High system compatibility Defoamer)
A high-quality defoamer for inks must be compatible with various resin systems, pigments, and additives, while providing quick foam suppression without causing haze or affecting gloss. It should also remain stable under different shear forces and temperature conditions during production and application. The ideal defoamer minimizes re-foaming, ensuring that inks maintain optimal flow and leveling properties from manufacturing to the final print.
Rickman defoamers are engineered to meet the stringent requirements of modern ink production and printing applications. They offer rapid foam knockdown, long-term stability, and excellent compatibility with diverse ink formulations. From pigment dispersion to final application, Rickman solutions help manufacturers achieve high-quality prints with improved efficiency and reduced waste.
Foam Control Solutions for the Pulp and Paper Industry
In the pulp and paper industry, foam is more than just a visual nuisance—it can slow down production, reduce product quality, and increase operating costs. During processes like pulping, bleaching, and paper machine operations, excessive foam interferes with the smooth flow of slurry, causes overflow, and even impacts sheet formation. This is why many mills rely on effective defoamer solutions to maintain productivity and ensure a consistent product.
Rickman defoamers are designed specifically to meet the challenges of the pulp and paper sector. Our formulations provide rapid foam knockdown, excellent persistence, and minimal impact on other process chemicals. Beyond product performance, Rickman offers comprehensive technical support, helping customers troubleshoot issues, optimize dosage, and adapt solutions to their unique process conditions. With advanced manufacturing capacity and a dedicated R&D team, we ensure consistent quality and reliable supply for partners worldwide.
Click on the related products links:RK-300P(High Antifoaming Performance Compound Defoamer)/RK-0010(High Efficiency Foam Control Agent)
Enhancing Construction Material Quality with the Right Defoamer
In the construction industry, the use of admixtures such as plasticizers, water reducers, and surfactants is essential to improve the performance of concrete, mortar, and other building materials. However, these chemical additives often introduce unwanted air into the mix, forming foam that can compromise the strength, surface finish, and long-term durability of structures. This makes defoamers a critical component in achieving consistent material quality.
Foam in cementitious systems can lead to surface defects, pinholes, and reduced compressive strength. Especially in self-leveling compounds, grouts, and high-performance concrete, entrapped air poses a serious threat to both aesthetics and structural integrity. Effective defoaming ensures smooth flow, optimal density, and improved compaction—all essential for modern construction requirements.
Construction-grade defoamers must be compatible with alkaline environments and exhibit excellent dispersibility in viscous systems. They should not delay setting time or impact curing behavior. Choosing the right defoamer helps not only reduce rework costs but also enhance the final appearance of flooring, precast components, and decorative surfaces.
Rickman defoamers are formulated to address these specific challenges. Our products offer rapid foam suppression, long-term stability, and excellent compatibility with a wide range of cement and gypsum-based systems. Whether for dry-mix mortar production or on-site concrete pouring, Rickman delivers high-performing solutions that reduce air entrainment without compromising the material’s properties.
What sets Rickman apart is not just our product performance—but also our service philosophy. Our team provides expert consultation to recommend the best formulation for your process, supports on-site testing, and ensures consistent supply with fast lead times. With Rickman, you’re not just buying a defoamer—you’re gaining a reliable partner in construction material optimization.
Click on the related products links:RK-04P(A High Efficiency Special Powder Antifoam) /RK-07P(High Cost-effective Defoaming Agent)
Controlling Foam for Effective Water Treatment The Role of Defoamers
Foam formation is a common challenge in various water treatment processes, including wastewater treatment, desalination, and industrial effluent management. Whether caused by biological activity, surfactants, or mechanical agitation, excessive foam can hinder oxygen transfer, disrupt sensor readings, and increase the risk of spillage or system inefficiencies. This makes the application of defoamers a vital step in maintaining safe, efficient, and regulation-compliant water treatment operations.
Beyond high-quality formulations, Rickman is committed to customer success through responsive technical support and customized service. Our team works closely with clients to understand specific foam issues and provide tailored solutions—backed by quick sample delivery, robust documentation, and flexible logistics. Whether you're optimizing an existing treatment line or developing a new facility, Rickman ensures a seamless, professional experience from consultation to implementation.
Click on the related products links:RK-500P(Polyether Defoamer For Paper Industry)/RK-1215A(Water-based Silicone Antifoam Agent)
Rickman defoamer products are tailored to meet the unique demands of the water treatment industry. Our formulations are engineered to deliver rapid foam knockdown and long-lasting suppression, even under high-shear and high-temperature conditions. From municipal wastewater plants to complex industrial recycling systems, Rickman defoamers offer excellent dispersibility and low residue impact, ensuring smooth processing and compliance with discharge standards.
Enhancing Construction Materials Performance with Effective Defoamers
Foam formation is a persistent issue in the construction materials industry, particularly in the production and application of concrete admixtures, mortar, putty, and gypsum-based systems. The presence of unwanted foam not only reduces the mechanical strength of the final product but also compromises its surface finish, workability, and durability. Addressing this challenge effectively is crucial to ensuring the reliability and quality of construction projects.
Beyond product performance, Rickman stands out through its responsive service and deep technical expertise. With a dedicated team focused on construction solutions, Rickman offers customized recommendations, rapid sampling, and formulation support. Our strong global logistics and reliable supply chain further ensure that customers get the right product, at the right time, for every project stage.
Click on the related products links:RK-800P(High Cost-effective Defoaming Agent For Concrete)/RK-600P(High Efficiency Cement Antifoam)
Rickman’s construction-grade defoamers are specifically engineered to meet the demanding requirements of modern building materials. Our products feature excellent foam control during both production and field application. Whether for dry-mix mortar, self-leveling compounds, or concrete admixtures, Rickman defoamers are designed to optimize dispersion, prevent air entrapment, and enhance compressive strength without compromising final aesthetics.
What are the techniques for military boots? -Molding process
Boots are a necessity in our daily lives. It can effectively protect our feet. In terms of military and police use, the requirements for military boots will be higher. It will require higher quality and durability than civilian boots. This is related to the production process of boots. The most commonly used technique in the military field is molding.
Today we- China Xinxing Guangzhou Imp&Exp Co., Ltd. will introduce the molding process of boots.
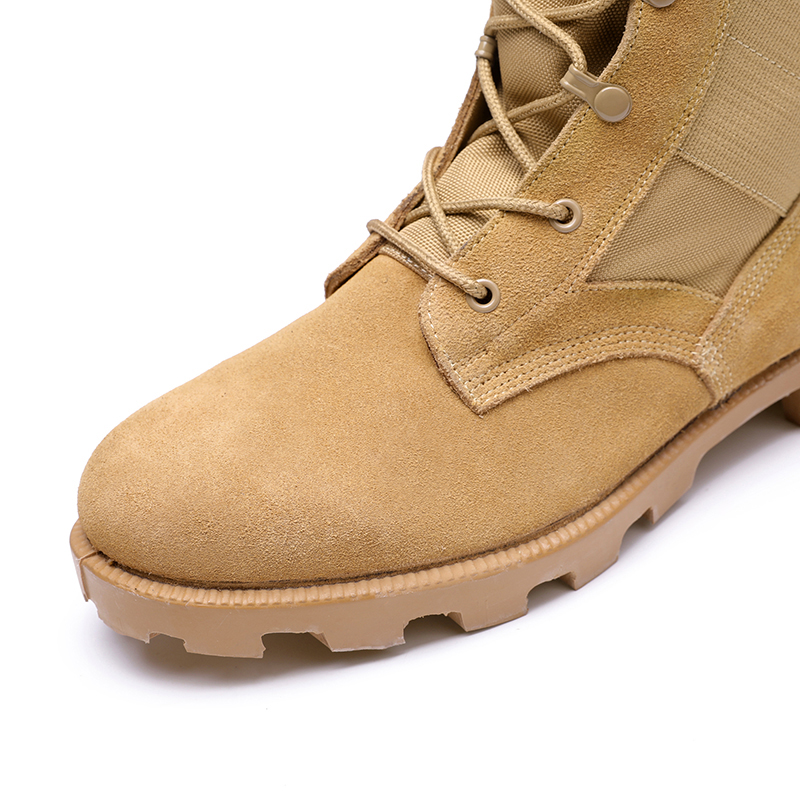
1.What is the molding process?
The molding process of boots is a common production technology that combines the sole and upper, mainly by heating and pressing the sole material (such as rubber, PU, PVC, etc.) directly vulcanized or bonded to the upper through a mold.
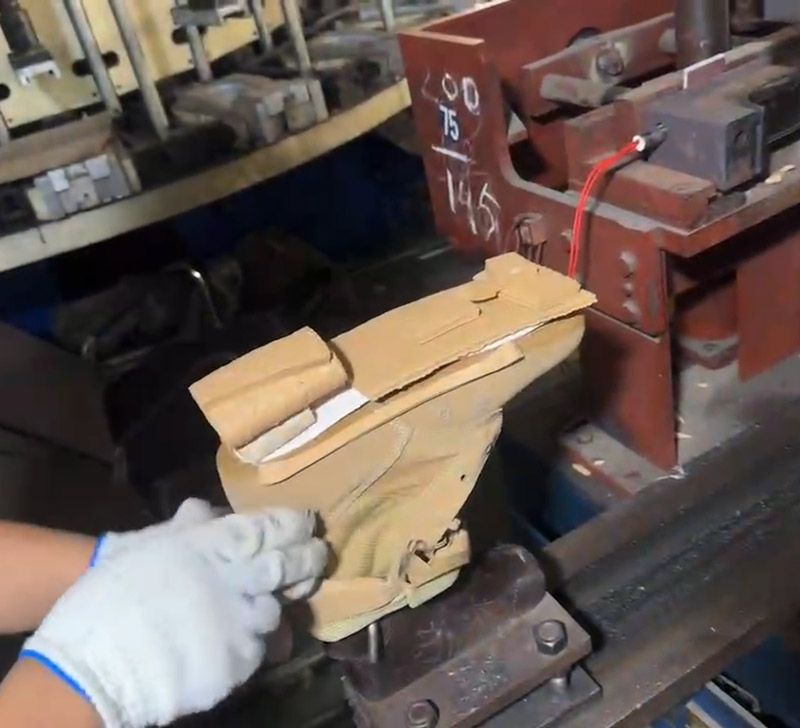
2.Basic process flow
Prepare the upper and shoe last: Place the upper over the shoe last to shape it and ensure it fits snugly with the foot.
Mold preheating: The metal mold is preheated to the required vulcanization or melting temperature of the material (usually around 150-160 ° C for rubber).
Insert sole material: Place raw rubber sheets, PU prepolymers, etc. at the bottom of the mold.
Compression molding: Align the shoe upper with the mold, close the mold under high pressure, and form the sole material in hot pressing while firmly bonding with the shoe upper.
Cooling and shaping: Cooling after demolding to complete solidification or vulcanization.
Advantage:
No need for additional adhesive, environmentally friendly and durable.
The pattern on the sole can be finely designed through molds (such as anti slip patterns).
Disadvantages:
The cost of customizing molds is high, and small batches are not economical.
High temperature and high pressure may limit certain surface materials (such as heat-resistant fabrics).
If you are interested in military boots. Please contact us promptly:mail@cxxgz.com. We have many product options for other type boots.
Looking forward your inquiry.
Why Durability Matters Materials Used in Modern Military Uniforms
Military uniform is the daily attire of soldiers from various countries. And the military uniforms of every country and every unit are of various types. But there won't be too much change in the material.
Today we- China Xinxing Guangzhou Imp&Exp Co., Ltd. will introduce the Materials Used in Modern Military Uniforms
1.Polyester (man-made fiber)
Polyester is the simplest synthetic fiber among the three, and its price is relatively cheap. It is a widely used synthetic clothing fabric in daily life. Its biggest advantage is its excellent wrinkle resistance and shape retention, making it suitable for outdoor products such as outerwear, various bags, and tents.
Advantages: High strength, super elasticity close to wool; Good heat resistance, light resistance, wear resistance, and chemical resistance;
Disadvantages: Poor staining, poor melting resistance, poor moisture absorption, and easy pilling and staining.
2.Cotton(natural fiber)
It refers to fabrics produced from cotton as raw material. Generally speaking, pure cotton fabric has good moisture absorption and heat resistance, and is comfortable to wear. Some industries with high requirements for moisture absorption of clothing can choose pure cotton fabric for processing. For example, summer school uniforms.
Advantages: Cotton fibers have good moisture absorption, high elasticity, heat and alkali resistance, and are hygienic and healthy;
Disadvantages: Easy to wrinkle, shrink, deform, and stick to hair
3.Nylon(man-made fiber)
Nylon, as the world's first synthetic fiber, has many outstanding advantages. It is very wear-resistant, more resistant to wear and tear than natural fibers such as cotton and wool, making it very suitable for making durable clothing and products, such as outdoor equipment, sportswear, etc. Meanwhile, nylon fabric has excellent elasticity, which can maintain its shape well and adapt to various movements, making it more comfortable to wear.
Advantages: Strong wear resistance, good elasticity, corrosion resistance, lightweight and easy to dry
Disadvantages: Poor moisture absorption, susceptibility to static electricity, poor heat and light resistance.
4.Aramid fiber(man-made fiber)
Aramid fiber, also known as "aromatic polyamide fiber", refers to long-chain synthetic polyamide fibers with over 85% of amide bonds directly attached to the benzene ring. Amide bonds are aromatic rings or derivatives of aromatic rings, and are a new type of special polymer material. There are currently two types of aramid fibers widely commercially produced in the market, namely meta aramid fibers and para aramid fibers.
Advantages: Good flame retardancy. Durable thermal stability. Generally used as flame retardant clothing for the Air Force.
Disadvantages: Aramid fibers have poor UV resistance. Aramid fiber is an expensive material with a price similar to carbon fiber.
The above are the main materials of modern military uniforms. Generally, it is made by combining artificial fibers with natural fibers in a certain percentage. Can achieve maximum cost-effectiveness. We also have a strong production line and accept customized services. Both fabric and uniform are acceptable.
If you are interested in this, please contact us promptly:mail@cxxgz.com.
Best regard!
The Ultimate Bedside Digital Alarm Clock with \"Power\
Meet the ultimate bedside companion Power: a tongyuanclock digital alarm clock that combines sleek design, modern functionality, and the convenience of wireless charging. Available in three vibrant hues—Yellow, Orange, and Purple—this stylish device is more than just an alarm clock; it’s the perfect blend of form and function, designed to enhance your daily routine.
Effortless Wireless Charging
Forget about the mess of tangled cords and welcome the simplicity of wireless charging. Power is equipped with a built-in wireless charger that works with any smartphone that supports wireless charging. Just place your phone on the charging pad and let the magic happen—no cables, no fuss, just pure convenience.
Clear and Customizable Digital Display
Power's LED digital display is bright and easy to read, making sure you’re always on time, whether you prefer a 24-hour or 12-hour format. It’s designed to keep you on track, even during those groggy early mornings.
Three Alarm Modes for Every Morning
Never worry about oversleeping again with three distinct alarm modes to choose from. Whether you need a gentle nudge or a more assertive wake-up call, Power ensures you start your day just the way you need to.
Adjustable Brightness for the Perfect Ambiance
Customize your bedroom’s ambiance with three levels of adjustable brightness. Whether you want a soft, warm glow or a brighter display, Power adapts to your preferences, making your space feel just right.
Extra Features: Date and Temperature at a Glance
Stay informed and in control with optional displays for the date and room temperature. A quick glance is all it takes to stay on top of your schedule and ensure your room is always at the perfect temperature.
Sleek, Modern Design
Power is not just about functionality; it’s a stylish addition to your bedroom decor. With its slim, modern design, it occupies minimal space on your bedside table while adding a touch of contemporary elegance to your room.
Achieving Surface Perfection in Coatings with Effective Defoamers
In the coatings industry, foam is more than a visual nuisance—it’s a performance disruptor. Whether during production, packaging, or application, uncontrolled foam can lead to surface defects such as craters, pinholes, and fish eyes. These issues not only compromise the aesthetic and functional properties of coatings but can also result in costly rework and reduced customer satisfaction.
Defoamers play a critical role in managing this challenge. By destabilizing and eliminating foam bubbles, these additives improve film formation, enhance leveling, and support consistent application performance. Selecting the right defoamer is essential, especially in modern water-based and high-solids systems, where formulation compatibility, recoatability, and long-term effectiveness are key considerations.
Rickman offers a comprehensive range of defoamer solutions specifically engineered for architectural coatings, industrial paints, and printing inks. From silicone-based to polymer-based systems, Rickman defoamers ensure rapid foam knockdown, excellent compatibility with various resin systems, and minimal impact on gloss or transparency. These products are formulated to maintain stability over storage and application, making them ideal for high-speed production and demanding end-use conditions.
What sets Rickman apart is not only its product performance, but also its technical support and service capability. With in-house R&D, industry-dedicated formulation guidance, and fast-response customer service, Rickman partners closely with coating manufacturers to tailor the right defoaming strategy for their formulations. Whether addressing microfoam during letdown or macrofoam during application, Rickman delivers solutions that improve coating quality and manufacturing efficiency.
Click on the related products links:RK-1100(Excellent anti-foaming performance Defoamer) /RK-8777(Outstanding anti-foaming performance Defoamer)